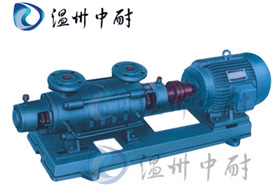
■ GC型臥式鍋爐給水多級泵產(chǎn)品概述:
GC型臥式鍋爐給水多級泵為臥式單吸多級分段式離心泵,主要用于鍋爐給水,所以又名鍋爐給水泵。該系列多級泵適于輸送溫度低于110°C的清水或物理化學(xué)性質(zhì)類似于水的無腐蝕性的其他液體,廣泛用于工礦企事業(yè)單位的鍋爐給水和城市生活供水。
■ GC型臥式鍋爐給水多級泵型號意義:
■ GC型臥式鍋爐給水多級泵產(chǎn)品特點:
1、水力模型先進(jìn),效率高,性能范圍廣。
2、泵運行平穩(wěn),噪音低。
3、軸封采用軟填料密封,安全可靠、結(jié)構(gòu)簡單,維修方便快捷。
■ GC型臥式鍋爐給水多級泵技術(shù)參數(shù):
流量:5-55m3/h;
揚程:46-301m;
功率:3-75KW;
轉(zhuǎn)速:2950r/min;
口徑:φ40-φ100;
溫度范圍:≤80℃;
工作壓力:≤2.7Mpa.
■ GC型臥式鍋爐給水多級泵結(jié)構(gòu)圖:
|
1 |
軸套螺母 |
2 |
軸承蓋 |
3 |
軸承 |
4 |
軸承體 |
|
5 |
軸承甲 |
6 |
填料壓蓋 |
|
7 |
填料環(huán) |
8 |
進(jìn)水段 |
|
9 |
密封環(huán) |
10 |
葉輪 |
|
11 |
中段 |
12 |
回水管 |
|
13 |
出水段 |
14 |
科衡環(huán) |
|
15 |
平衡盤 |
16 |
尾蓋 |
|
17 |
軸套乙 |
18 |
拉緊螺栓 |
|
19 |
軸 |
20 |
園螺母 |
■ GC型臥式鍋爐給水多級泵結(jié)構(gòu)說明:
GC型鍋爐給水泵為多級分段式,11/2 GC- 4GC四個型號的進(jìn)出口分別在進(jìn)水段和出水段上,均垂直向上,其揚程可根據(jù)使用需要而增減水泵級數(shù)。水泵裝配良好與否,對性能影響很大,尤其是各個葉輪的出口與導(dǎo)翼進(jìn)口之相對位置,每吸葉輪的吐出口中心必須對準(zhǔn)導(dǎo)翼的中心,其中稍有偏差即將使水泵的流量減少,揚程降低,效率差,故在檢修后裝配時務(wù)必注意,若有偏差必須調(diào)整。
Gc型多級泵的主要零件有軸、軸套、進(jìn)水段、葉輪、導(dǎo)翼、密封環(huán)、中段、出水段、平衡環(huán)、平衡盤、尾蓋。
進(jìn)水段、中段、出水段及尾蓋均為鑄鐵制成,共同形成泵的工作室。
葉輪為鑄鐵制成,內(nèi)有葉片,液體沿軸向單側(cè)進(jìn)入,由于多級泵葉輪前后受壓不等,必須存在軸向力,此軸向力由平衡盤來承擔(dān),葉輪制造時經(jīng)靜平衡試驗。
軸為優(yōu)質(zhì)碳素鋼制成,中間裝有葉輪,用鍵、軸套和軸套螺母固定在軸上。軸的一端按裝聯(lián)軸器部件,與電機直接聯(lián)接。從轉(zhuǎn)動方向看時,泵軸為川頁時針方向旋轉(zhuǎn)。
密封環(huán)為鑄鐵制成,防止水泵中高壓水漏回進(jìn)水部分,分別固定在化工泵進(jìn)水段與中段之中,為易損件,磨損后可用備件更換。
離心泵平衡環(huán)為鑄鐵制成,固定在出水段上,它與平衡盤共同組成平衡裝置。
平衡盤為耐磨鑄鐵制成,裝在軸上,位于出水段與尾蓋之間,平衡軸向力。
化工泵軸套為鑄鐵制成,位于兩填料室處,離心泵作固定葉輪和保護(hù)泵軸之用。為易損件,磨損后可用備件更換。
軸承是用單列向心球軸承,采用鈣基黃油潤滑。
填料起密封作用,防止空氣進(jìn)入和大量液體漏出。
填料密封由進(jìn)水段和尾蓋上的填料室,填料壓蓋,填料環(huán)及填料等組成,少量高壓水流入填料室中起水封作用。填料的松緊程度必須適當(dāng),不可壓的太緊,也不可太松,以液體能一滴一滴地滲出為準(zhǔn)。如果填料太緊,軸套容易發(fā)熱同時耗費功率。填料太松,由于液體流失要降低水泵效率。
■ GC型臥式鍋爐給水多級泵產(chǎn)品用途:
GC型臥式鍋爐給水多級泵特別適用于小型鍋爐給水,也可廣泛應(yīng)用于壓力容器供水、熱水循環(huán)、高層建筑給水、農(nóng)田灌溉、消防增壓、水力沖洗、食品、釀造、醫(yī)藥、化工、水產(chǎn)養(yǎng)殖、環(huán)境保護(hù)、化工工藝流程及機床配套等各行業(yè),作為給水排水的動力設(shè)備。
■ GC型臥式鍋爐給水多級泵性能參數(shù):
型號 |
流量 |
揚程 |
轉(zhuǎn)速 |
效率 |
功率(KW) |
|
軸功率 |
電機功率 |
|||||
1.5GC-5×2 |
6 |
46 |
2950 |
38 |
2 |
3 |
1.5GC-5×3 |
6 |
69 |
2950 |
38 |
3 |
4 |
1.5GC-5×4 |
6 |
92 |
2950 |
38 |
4 |
5.5 |
1.5GC-5×5 |
6 |
115 |
2950 |
38 |
5 |
7.5 |
1.5GC-5×6 |
6 |
138 |
2950 |
38 |
6 |
7.5 |
1.5GC-5×7 |
6 |
161 |
2950 |
38 |
7 |
7.5 |
1.5GC-5×8 |
6 |
184 |
2950 |
38 |
8 |
11 |
1.5GC-5×9 |
6 |
207 |
2950 |
38 |
9 |
11 |
2GC-5×2 |
10 |
64 |
2950 |
39.6 |
4.4 |
7.5 |
2GC-5×3 |
10 |
96 |
2950 |
39.6 |
6.6 |
11.0 |
2GC-5×4 |
10 |
128 |
2950 |
39.6 |
8.8 |
15.0 |
2GC-5×5 |
10 |
160 |
2950 |
39.6 |
11.0 |
15.0 |
2GC-5×6 |
10 |
192 |
2950 |
39.6 |
13.2 |
18.5 |
2GC-5×7 |
10 |
224 |
2950 |
39.6 |
15.4 |
22.0 |
2GC-5×8 |
10 |
256 |
2950 |
39.6 |
17.6 |
30.0 |
2GC-5×9 |
10 |
288 |
2950 |
39.6 |
19.8 |
30.0 |
2.5GC-6×2 |
15 |
62 |
2950 |
43.7 |
5.8 |
11.0 |
20 |
54 |
2950 |
47.4 |
6.2 |
11.0 |
|
2.5GC-6×3 |
15 |
93 |
2950 |
43.7 |
8.7 |
15.0 |
20 |
81 |
2950 |
47.4 |
9.3 |
15.0 |
|
2.5GC-6×4 |
15 |
124 |
2950 |
43.7 |
11.6 |
22.0 |
20 |
108 |
2950 |
47.4 |
12.4 |
22.0 |
|
2.5GC-6×5 |
15 |
155 |
2950 |
43.7 |
14.5 |
22.0 |
20 |
135 |
2950 |
47.4 |
15.5 |
22.0 |
|
2.5GC-6×6 |
15 |
186 |
2950 |
43.7 |
17.4 |
30.0 |
20 |
162 |
2950 |
47.4 |
18.6 |
30.0 |
|
2.5GC-6×7 |
15 |
217 |
2950 |
43.7 |
20.2 |
30.0 |
20 |
189 |
2950 |
47.4 |
21.7 |
30.0 |
|
2.5GC-6×8 |
15 |
248 |
2950 |
43.7 |
23.2 |
37.0 |
20 |
216 |
2950 |
47.4 |
24.8 |
37.0 |
|
2.5GC-6×9 |
15 |
279 |
2950 |
43.7 |
26.1 |
22 |
20 |
243 |
2950 |
47.4 |
27.9 |
22 |
|
4GC-8×2 |
30 |
86 |
2950 |
51 |
13.8 |
30 |
45 |
82 |
2950 |
60 |
16.8 |
30 |
|
55 |
76 |
2950 |
62.5 |
18.1 |
30 |
|
4GC-8×3 |
30 |
129 |
2950 |
51 |
20.7 |
37 |
45 |
123 |
2950 |
60 |
25.2 |
37 |
|
55 |
114 |
2950 |
62.5 |
27.2 |
37 |
|
4GC-8×4 |
30 |
172 |
2950 |
51 |
27.6 |
55 |
45 |
164 |
2950 |
60 |
27.6 |
55 |
|
55 |
152 |
2950 |
62.5 |
36.2 |
55 |
|
4GC-8×5 |
30 |
215 |
2950 |
51 |
34.5 |
55 |
45 |
205 |
2950 |
60 |
42.0 |
55 |
|
55 |
190 |
2950 |
62.5 |
45.3 |
55 |
|
4GC-8×6 |
30 |
258 |
2950 |
51 |
41.4 |
75 |
45 |
246 |
2950 |
60 |
50.4 |
75 |
|
55 |
228 |
2950 |
62.5 |
54.1 |
75 |
|
4GC-8×7 |
30 |
301 |
2950 |
51 |
48.2 |
75 |
45 |
287 |
2950 |
60 |
58.8 |
75 |
|
55 |
266 |
2950 |
62.5 |
63.4 |
75 |
|
4GC-8×8 |
30 |
344 |
2950 |
51 |
55.0 |
100 |
45 |
328 |
2950 |
60 |
67.0 |
100 |
|
55 |
304 |
2950 |
62.5 |
73.0 |
100 |
|
4GC-8×9 |
30 |
387 |
2950 |
51 |
62.0 |
100 |
45 |
369 |
2950 |
60 |
75.5 |
100 |
|
55 |
342 |
2950 |
62.5 |
82.0 |
100 |
|
4GC-8×10 |
30 |
430 |
2950 |
51 |
69.0 |
- |
45 |
410 |
2950 |
60 |
84.0 |
- |
|
55 |
380 |
2950 |
62.5 |
91.0 |
- |
■ GC型臥式鍋爐給水多級泵裝卸、啟動、運轉(zhuǎn)與停止:
1、裝卸順序
1) 將密封環(huán)〈9〉緊裝在進(jìn)水段(8〉上。
2) 將裝好軸套甲〈5〉和鍵的軸〈9〉穿過進(jìn)水段〈8〉并推入葉輪(10),并在中段上輔一張紙墊,裝上中段(11),再推入第二個葉輪,重復(fù)以上步驟將所有的葉輪及中段裝完。
3) 將平衡環(huán)(14〉,裝在出水段〔13〉上。
4) 將出水段〈13〉裝到中段上,然后用拉緊螺栓〈18〉將進(jìn)水段、中段和出水段緊固在一起。
5) 裝上平衡盤〈15 〉及軸套乙〈17 〉。
6) 將紙墊裝在尾蓋上,將尾蓋裝到出水段上,并將填料及填料環(huán)(7),填料壓蓋(6)順次裝入進(jìn)水段和尾蓋的填料室。
7) 將軸承體〈4〉分別裝到進(jìn)水段和尾蓋之上,并用螺栓緊固。
8) 裝入滾珠軸承〈3 〉,并分別以軸套螺母〈1 〉與園螺母〈20 〉緊固。
9) 在軸承體內(nèi)裝入適量的黃油,并將紙墊套在軸承蓋(2 〉上,將軸承蓋裝到軸承體上以螺釘緊固。
10) 裝上回水管,聯(lián)軸器部件及所有的四方螺塞。
11) 拆卸按上述步驟相反進(jìn)行。
安裝:
安裝前的準(zhǔn)備工作:
1)檢查水泵和電機;
2)準(zhǔn)備工具及起重機械;
3)檢查機器的基礎(chǔ);
2、安裝順序
1) 整套水泵運到現(xiàn)場,附帶底座者已裝好電動機。找平底座時,可不必卸下水泵和電機。
2) 將底座放在地基上,在地腳螺釘附近墊楔形鐵塊,將底座墊高約20-40毫米準(zhǔn)備找平后填充水泥之用。
3) 用水平儀檢查底座的水平底,找平后搬緊地腳螺母,用水泥將填充底座。
4) 經(jīng)3-4天水泥干固后,再檢查一下水平度。
5) 將底座的支持平面,水泵腳及電機腳的平面上的污物清洗除凈,并把電機和水泵放在底座上。
6) 調(diào)整泵軸水平。找平后,適當(dāng)上緊螺母,以防走動,于調(diào)節(jié)完畢后再安裝電動機、在不合水平處墊以鐵板,泵和聯(lián)軸器之間留有一定間隙。
7) 把水平尺放在聯(lián)軸器上,檢查水泵軸心線與電機軸心線是否重合,若不重合,在電機和泵的腳下墊以薄鐵片,使兩個聯(lián)軸器外園與平尺相平,然后取出墊的幾片薄鐵片, 在經(jīng)過刨制的整塊墊板來代替鐵片,并重新檢查安裝情況。
為了檢查安裝的精度。在幾個相反位置上用塞尺,測量兩聯(lián)軸器平面的間隙,聯(lián)軸器平面一周上大和小間隙差數(shù)不得超過0.3毫米,兩端中心線上下或左右的差數(shù)不得超過0.1毫米。
3、起動及停止:
1.將軸上及其它涂油件上所涂的油除凈。
2.用汽油清洗軸承和軸室,用棉紗擦凈。
3.在軸承體內(nèi)加入鈣基黃油。
4.試驗起動。開動電機,檢查電機旋轉(zhuǎn)方向,嚴(yán)禁水泵反轉(zhuǎn)而使軸套螺母松開。
5.往泵內(nèi)注水或用真空泵引水。
6.關(guān)閉吐出管上的閥及壓力計旋塞。
7.上述過程完畢后,啟動電機,打開壓力計旋塞。
8.當(dāng)水泵以正常轉(zhuǎn)數(shù)運轉(zhuǎn)時,壓力計顯示適當(dāng)壓力,然后打開真空表旋塞并逐漸打開排水管路上的閘閥直到需要的壓力為止。
9.當(dāng)停止水泵時,要慢慢地關(guān)閉排水管路上的閘閥,關(guān)閉真空表旋塞。并停止電機,然后關(guān)閉壓力表旋塞。
10.長期停止使用水泵時,水泵應(yīng)拆卸開,將泵另件的水擦干,并在滑動面上涂以防銹油妥善保存。
運轉(zhuǎn):
1.注意水泵軸承溫度,不得超過外界溫度35℃。其極限溫度不得大于75℃。
2.水泵在運轉(zhuǎn)時,時常注意加油。
3.填料室內(nèi)正常漏水程度,以每分鐘10-20滴為準(zhǔn),應(yīng)隨時調(diào)整填料壓蓋壓緊程度。
4.定期檢查聯(lián)軸器,注意檢查電機軸承溫升。
5.運轉(zhuǎn)過程中,如發(fā)生噪音或異常的聲音時,應(yīng)立即停車檢查其原因。